As most of you know who have been reading this blog for a while, quite a lot of the most admired vintage audio gear (like my vintage McIntosh), and desired vintage electric guitars & their amps, used tinned-copper internal wiring, and it was at least partly responsible for that desirable 'vintage tone' that so many of us enjoy about them.
Back in 1950's America, tinned-copper wire was used in commercial applications because electroplating copper wires with tin prevented corrosion and improved stripability, which made for an altogether more durable & reliable wire for commercial use.
Corrosion was an issue back in the 1950's because the common insulators of the day released sulfur peroxide over time, which would then react with the copper conductors to form copper sulfide, which degraded the wires' performance. However, if you tinned the copper wire, the sulfur peroxide released from the insulators couldn't degrade the copper by forming copper sulfide, thus protecting the performance characteristics of the cables.
When the wire manufacturers figured out how to make insulators that didn't degrade over time, the need for tinned-copper wire diminished in commercial applications, and accountants with a watchful eye on companies' bottom lines quickly vetoed the more expensive tinned-copper cabling for the cheaper standard copper cabling.
When the audio and electric guitar industries made the change from tinned-copper to regular copper, at first no one said anything.
Then musicians began to realize that the regular copper wiring was a big step backwards musically from the tinned-copper wiring they were used to in their guitars and guitar amplifiers, word got out, and the musicians began stripping the standard copper wiring out and putting back in the tinned-copper wiring to restore musicality.
A cottage industry soon arose in the guitar world providing the tinned-copper wiring, capacitors like Bumblebees and Black Beauties, and Allen Bradley carbon composition resistors to restore guitars to their 'vintage tone' musicality.
Now even guitar companies have recognized this trend, and are offering tinned-copper cabling in select higher end models and special editions.
It took a little longer for us audio guys to figure out what had happened to the music, and why things were sounding less musically engaging for us, but it essentially boils down to the same sort of thing as with the guitar world.
With a shift away in electronics from tinned-copper wiring, from capacitors & resistors with good tone, like Bumblebee's and Allen Bradley's, the musicality of much of the modern hifi gear diminished.
A lot of us audio nuts and music lovers didn't like what we were hearing from most of modern hifi, but we really weren't fully sure about the why of it.
For me, there was a bit of serendipity in play when Yazaki-san turned me onto using vintage Western Electric WE16GA wire for my Tannoy Westminster Royal SE loudspeakers' internal & crossover wiring, and as speaker cables, and using the old studio standby Belden 8402 microphone cable as interconnects, both of which share in common tinned-copper conductors.
The WE16GA / Belden 8402 adventure was a significant milestone for me, as it marked my entering a whole new world of mindfulness in recognizing the contribution that 'vintage tone' made to my music listening.
I began to experience unprecedented levels of 'realness' in musicality, in terms of timbral realism, accuracy & resolution of tone color, compelling portrayals of dynamics, tempos, beats, melodies, rhythms, and perhaps most importantly, a big improvement in being able to connect with the artists musical intentions, which resulted in a significantly improved emotional connection to the music.
Then, while doing adventures with my vintage McIntosh MC30 monaural amplifiers with Yazaki-san and Ron-san, I realized all my vintage McIntosh gear was wired up with vintage Western Electric tinned-copper cabling internally.
In short, thanks to Yazaki-san's influence, I discovered for myself what the electric guitar guys realized about tinned-copper 'tone-wire' before me, that it brings the music to life in incredibly musically meaningful 'real' ways, and restores part of what was lost to the sands of time as technology marched forward.
Finally, when Yazaki-san sent me some headshell leads made of Western Electric 24-gauge solid-core wire, and I experienced what a dramatic difference tinned-copper headshell leads could make to overall musicality, I was rather stunned, because it turned out those short little tinned-copper headshell wires made as much difference (or maybe more) as do speaker cables, interconnects, and power cords.
The Duelund DCA26GA Tinned-Copper Solid-Core Wire
That brings me to the topic of this post, the headshell leads I just made from the new Duelund DCA26GA tinned-copper solid-core wire, which Frederik just released a few days ago.
Headshell wires are probably the easiest DIY wire project there is, as all you do is solder the wires into the ends of the clips and you're done.
I don't claim to be any sort of expert on making headshell leads, or having the last word on how to do it, but I can share a few tips I've learned along the way with you, as well as some things I still need to figure out.
I'm learning each time I make a set of headshell leads, and I'll continue to share with you what I learn as I go.
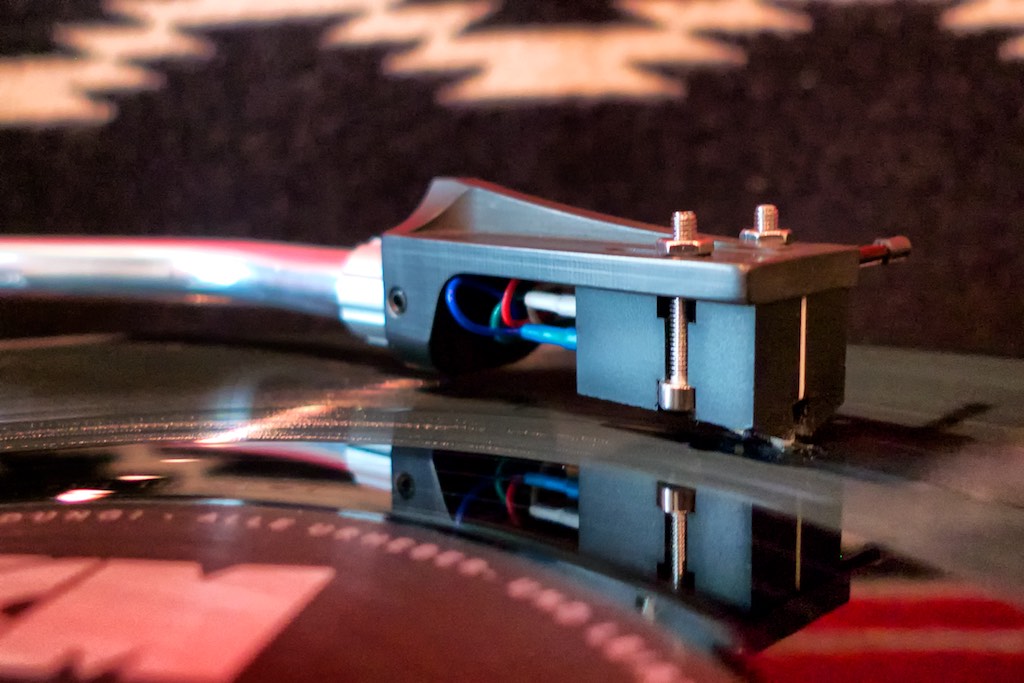
Denon DL103 stereo phono cartridge mounted to Thomas Schick headshell. Notice the skinny, looping stock headshell leads.
When you look at the normal skinny headshell leads that come stock with most headshells, you'll notice they're skinny and flexible things that bend around easily as you attach them to the cartridge & headshell pins, as in the photo above with the Thomas Schick graphite headshell that I enjoy so much.
The typical length of a headshell wire from clip-to-clip is smidgen over one and three-quarter inches, or about 45 mm.
Tip # 1: The closer you stay to that 1¾ inch (45mm) length, the easier your life will be when trying to install your new DIY headshell leads on your headshell and cartridge pins.
If you look closely at the photo above you'll notice that the Cardas headshell clip is approximately half an inch long (~13mm). That means the clips on each end of the wire take up more than half (~26mm) the total length (~45mm) of the headshell lead.
So the actual tinned-copper conductor is only a smidgen over three-quarters of an inch (~19mm) in length, with just enough wire exposed to solder into the barrel of the cartridge clip.
Tip # 2: I found the easiest way to solder up the clip/wire interface was to use a helping hand tool to hold the clip, then insert the solder wire into the clip barrel, then heat the clip until the solder melts and fills the clip barrel.
After I removed a bit of cotton dielectric on the ends to expose a bit of the tinned-copper wire, I held the DCA26GA wire in my hand while heating heating the clip with the soldering iron in my other hand, and as soon as the solder in the clip barrel became molten I inserted the wire tip into the barrel with the molten solder, and then let it cool.
Repeat for each clip/wire interface a total of eight times, and you've got a set of four DCA26GA headshell leads!
Tip # 3: The conductor in the Duelund DCA26GA is fine and can be rather fragile. I broke the headshell wires I made trying to install them four different times. I snapped them off at the clip once, and more towards the middle of the lead three times.
In the photos you see the headshell leads as a linear wires, but I found I had much better results when I "pre-looped" the headshell lead wires before soldering, as it removed the need to do that during installation on the headshell & cartridge pins, which put too much stress on them.
That made it much easier to install the leads on the pins without breaking them, by building in a little 'give' thanks to the loop.
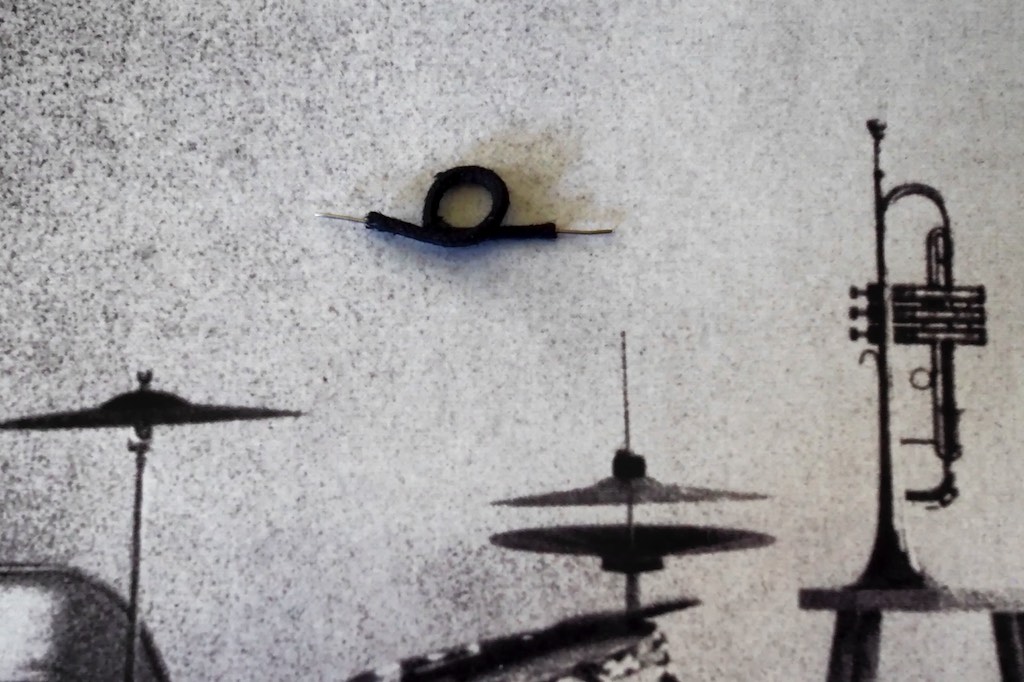
Looping the DCA26GA before soldering helps prevent breakage when installing on cartridge/headshell pins.
Tip # 4: Once you get the new leads in place don't touch them! Remember these are fragile bits of wire, and the more you handle them the more often you will break them. That's an unavoidable hazard for me as an audio writer who has to swap things in and out all the time for comparisons, but you'd be best to avoid it if you can.
One thing I haven't yet figured out is a good solution for wrapping the ends of the headshell leads to cover the frayed cotton edges of the dielectric.
As you can see in the photos, I used small bits of Peavey microphone tape to wrap the ends in the two sets of headshell leads I've made, but it doesn't work well for that purpose, and it tends to come undone.
I think I should probably take a page from Mr. Steen Duelund's playbook, and wrap the ends with a natural material rather than something made of a synthetic material like the Peavey tape or shrink-fit tubing.
I'm thinking that natural brown kraft paper about the same thickness as normal printer paper (28/70#) could work pretty well, with its natural pulp fibers, could be a pretty good choice.
I'd have to cut thin strips to glue in place, probably with wood glue of some sort. Sounds tedious.
I suppose an easier alternative would be trim the frayed cotton ends off evenly, then carefully seal the ends with a bit of wood glue.
If you have any good ideas on this front be sure to let me know!
First Listening Impressions of the Duelund DCA26GA Tinned-Copper Single-Core Headshell Leads
Prior to listening to the Duelund DCA26GA headshell leads I just made, I wanted to establish baseline listening impressions with the Art of Tone 22 gauge tinned-copper solid-core headshell leads I made just a few days ago.
At first my DIY Art of Tone headshell leads had a bit of that pre-run-in roughness that I have come to expect from tinned-copper, but now with a few days of time on them they have really settled in very nicely, and I really like what I'm hearing from them.
My Art of Tone headshell leads have in spades the relaxed musicality, beautifully rendered timbral realism, accuracy & resolution of tone color, compelling portrayals of dynamics, tempos, beats, melodies, and rhythms, that I've come to expect from tinned-copper wires, and those traits combined with a rich and naturally warm presentation makes them absolutely captivating to listen to, and they sound ravishingly good from an emotional standpoint.
The way the Art of Tone headshell leads have allowed me to relax into and connect with the artists' musical intentions is an unparalleled emotional experience for me, outdoing even the impressive Western Electric WE24GA headshell leads in that regard.
Given how good the Art of Tone headshell leads play music, I really wanted to give my brand new DIY Duelund DCA26GA headshell leads a listen.
Given these are first impressions, with no run-in time on my new DIY Duelund DCA26GA headshell leads at all, I expected that they would sound a little rough at times, just as my Art of Tone DIY headshell leads did at first (and Western Electric WE24GA did before them), and they did sound a bit rough at times, but overall I was very impressed with what I heard.
Compared to my Art of Tone headshell leads, the Duelund DCA26GA headshell leads were more transparent sounding, with more details & nuance being apparent, a more spacious & obvious soundstage, and with images that were more vividly portrayed in space.
On well recorded & produced albums, the Duelund DCA26GA headshell leads were stunning with their immense sense of space, their presentation of musical nuance in timbral textures, and their vivid imagery.
The Duelund DCA26GA headshell leads don't (yet?) have the warmth or relaxed musicality of my run-in Art of Tone headshell leads, and they are more neutral, forward, and direct sounding in comparison.
Three data points are enough for statistics, but not necessarily enough for conclusions, but I did notice one trend when comparing the 22 gauge Art of Tone, the 24 gauge Western Electric, and the 26 gauge Duelund tinned-copper solid-core wire as headshell leads.
The obvious trend was that as the gauge got fatter, the overall presentation became warmer sounding, with the Art of Tone being the warmest, the Western Electric being slightly less warm, and with the Duelund being the least warm of the three. The Duelund DCA26GA was closer to being neutral sounding than the other two, but still had a touch of natural warmth.
The 22 gauge Art of Tone headshell leads are more information rich than the WE24GA headshell leads, and have an intoxicating silkiness, naturalness, and sense of nuance to them that I find very satisfying and emotionally stimulating. The WE24GA sounds a bit muted & veiled compared to the Art of Tone headshell leads, with the Duelund DCA26GA easily being the most transparent and detailed of the three.
All of these tinned-copper headshell leads do a beautiful job of presenting a sense of believable timbral realism, accuracy & resolution of tone color, compelling portrayals of dynamics, tempos, beats, melodies, and rhythms, that I've come to expect from tinned-copper wires.
In this group of three there are no losers, and the traits of each could make it a best choice for a particular voicing situation.
I'll have more to say about the Duelund DCA26GA headshell leads after I get some more run-in time on them.
I suspect the Duelund DCA26GA will smooth out and get more natural sounding with some run-in time on them, as is common with tinned-copper wires, and if that happens to the degree that I think it might, then they will be truly profound as headshell leads.
One thing I can say, is that if you're still using regular ol' stock headshell leads you really need to build up some tinned-copper headshell leads and give them a listen.
Tinned-copper headshell leads are certainly the lowest cost, and one of the biggest single improvements you can make to your vinyl front end.
Highly recommended!
I'm also thinking about other applications for the Duelund DCA26GA, like replacing the internal wireing of my SPU phono cartridges with it, as tonearm leads, or perhaps even internal tonearm wiring. I also think it would be interesting to build a set of regular RCA interconnects out of DCA26GA and see how that sounds. Maybe even shielded DCA26GA interconnects for use with a SUT?
Duelund DCA26GA tinned-copper wire is available now from hifi collective in the UK here.
¸¸.•*¨*•♫♪¸¸.•*¨*•♫♪¸¸.•*¨*•♫♪
I really want to thank Frederik Carøe for the all the effort and expense he's gone to in manufacturing a full line of Duelund Coherent Audio tinned-copper cables, the DCA12GA, the DCA16GA, the DCA20GA, and now the DCA26GA solid-core.
I truly appreciate Frederik for being so daring in re-introducing music lovers and hifi nuts to the wonders of tinned-copper cabling in contemporary audio, which I think is a very big deal if you want to experience the very substantial best that audio has to offer to the music lover.
¸¸.•*¨*•♫♪¸¸.•*¨*•♫♪¸¸.•*¨*•♫♪
As always, thanks for stopping by, and may the tone be with you!