I love surprises, and particularly surprises like the ones sent to me by Frederick Carøe at Duelund Coherent Audio in Denmark!
When I first opened the box from Frederik, what did I see? I was looking through squinty, blurry eyes, and I was like, "Wow! Frederik sent me a whole box of Cuban cigars! How cool is that! Man, what a great guy!"
As I focussed in a little better and read the labels, I realized that, no, those were not Cuban cigars, but in fact Frederick had sent me a box full of prototype tinned-copper 0.22uF Duelund Coherent Audio CAST capacitors!
A totally awesome surprise, and much healthier than Cuban cigars! A huge "Thank you!" to Frederik for such a fantastic surprise!
Now about those clues from Frederik about the identity of the surprise: In spite of the three clues that Frederik sent me as to the identity of the surprise (below), I was in fact quite clueless as to what to what was pictured in each photo, and what kind of surprise the three clues might add up to be.
Clue 1 is the tinned-copper foil that is wound with the dielectric during the construction of the CAST capacitors.
Clue 2 is photo of the mylar/paper dielectric in wax that Frederik used to make the prototype capacitors.
Finally, Clue 3 is the Duelund DCA16GA tinned-copper wire that is used for the leads in the prototype tinned-copper CAST capacitors.
So Clues 1, 2, and 3 add up to reveal the identity of the prototype tinned-copper 0.22uF Duelund Coherent Audio CAST capacitors!
This is the first public appearance of the prototype 0.22uF Duelund Coherent Audio CAST tinned-copper capacitors, and no one on Planet Earth has yet heard them, not even Frederik!
I feel incredibly honored & humbled that I will be the first person to put an ear to these prototype tinned-copper capacitors to hear what they can do!
Frederik told me that I could use them in loudspeaker and electronics applications up to about 400v or so, which means I'll be able to try them in the breadboard crossovers I'm building for my vintage Altec A5 Voice of the Theatre loudspeakers, as well as in the modifications Ron and I performed on my vintage McIntosh electronics.
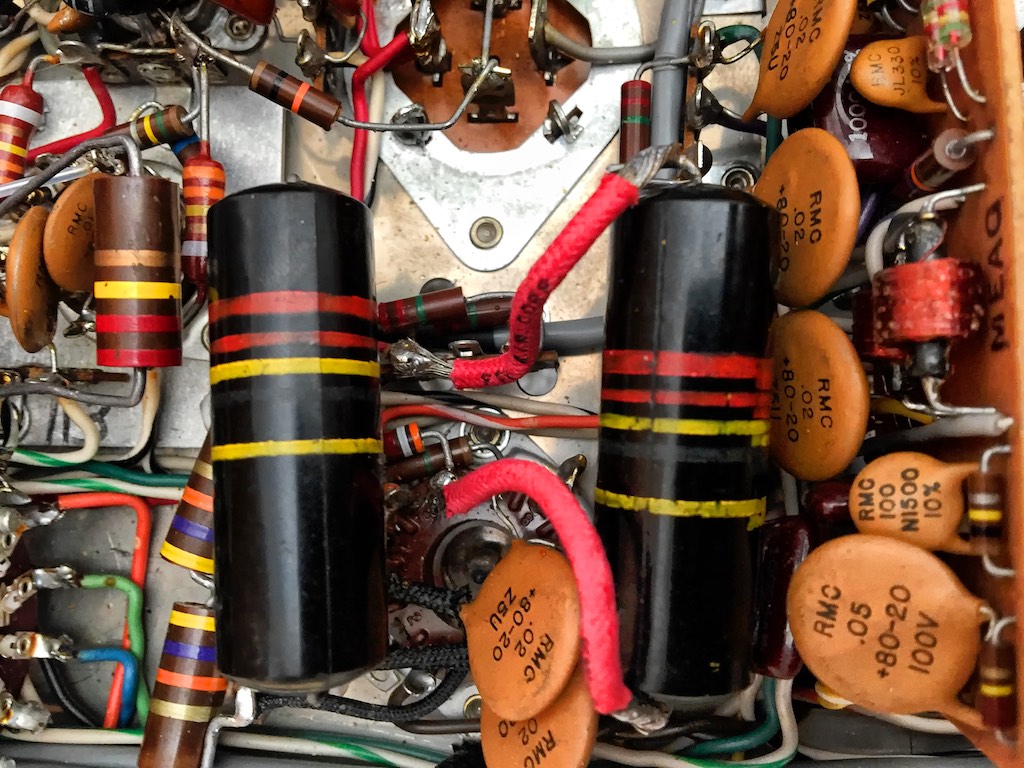
Vintage 0.22uF Bumblebee caps in my vintage McIntosh MX110Z tuner-preamplifier in the first stage cathode follower of the high level input.
This is going to be exciting, and I'll look forward to telling you all about the results of my trials using the prototype 0.22uF Duelund Coherent Audio CAST tinned-copper capacitors!
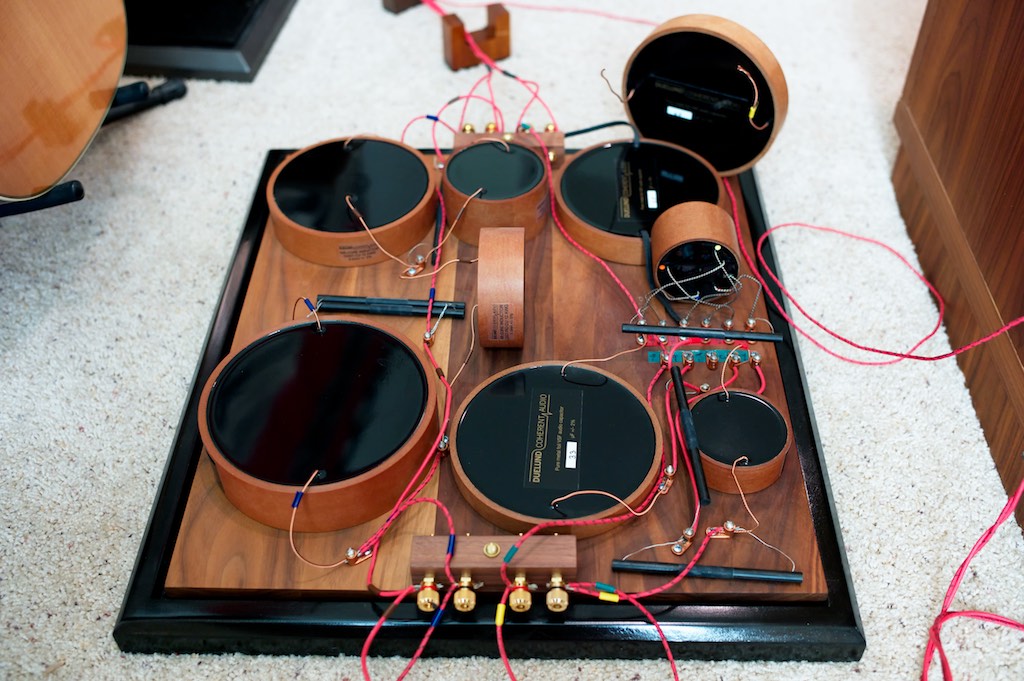
The Duelund CAST crossovers we built for my Westminster's in the Duelund-WRSE project that I wrote about for Positive Feedback.
For those of you who have come to my blog after I wrote about the Duelund Coherent Audio CAST capacitors, inductors, resistors, and autoformers, that Frederik and I used to build custom external crossovers for my Tannoy Westminster Royal Special Edition loudspeakers (Positive Feedback Issue 70 and Issue 74), and the beyond mind-blowing results we achieved, I want to give you a little recap of what is so special about the Duelund approach to building their handcrafted CAST capacitors.
I've said it numerous times here at Jeff's Place, that after my experiences with the Duelund-Westminster project crossovers, it is my opinion that the Duelund Coherent Audio CAST capacitors that are hand-crafted by Frederik and his team in Denmark are the finest audio capacitors made in the world today by quite a large margin, and I know many of you reading this right now that have experience with the Duelund CAST components, are nodding your heads in affirmation.
Each tinned-copper Duelund CAST capacitor is completely hand-made in an incredibly labor intensive process.
First the foils of tinned-copper are wound with the Mylar/paper dielectric to a certain value that is a good deal over the needed capacitance.
Then the winding is put under high vacuum pressure in a wax tank at high temperature for about a week, so that everything inside the winding undergoes vacuum impregnation and is permeated by wax.
When this process is done, the resulting foil is wound by hand in a humidity and temperature-controlled room to an exact specification, and then it is placed back into the wax.
Immediately after this process the winding is sealed by the use of a special lacquer to seal against moisture. This takes another week.
During this process a ring of vacuum impregnated paper has been readied with a base of the CAST material.
The winding is heated and then placed in the ring & base assembly and CAST material is poured on top of it in five stages, with air bubbles in the CAST material being forced out by applying a very precisely controlled flame to the surface. This process takes another week.
Following this step the capacitor is given a final measure and check. The total production time is typically six to eight weeks.
I'll be thinking about which project I want to try the prototype 0.22uF Duelund CAST tinned-copper capacitors in first, and then we'll give them a listen. It should be fun!
***
I've now got a pair of prototype 0.22uF Duelund CAST tinned-copper capacitors on my audiodharma Cable Cooker™ getting ready for their maiden voyage. I figure four days should be a good starting point for conditioning on the Cooker™.
I'm thinking my first trial with the prototypes should be in my vintage McIntosh MX110Z tuner-preamplifier, to see how well the 0.22uF Duelund CAST tinned-copper capacitors fare against the Jupiter Condenser Red Astron's tinfoil caps I now have in the first stage cathode follower of the high level input.
As always, thanks for stopping by, and may the tone be with you!